Nitinol’s ability to undergo extreme deformations and return to an intended shape (superelasticity) has made it a critical material in trans-catheter medical devices. This remarkably flexible structural metal has made it possible to deliver complicated end effectors, stents, heart valves, and other minimally invasive implants and tools through ever smaller catheters, making possible implants that change with the human body.
Since its discovery in the 1960s, Nitinol has transformed the field of catheter-based medical devices. Today, Resolution continues to push the boundaries of this extraordinary material, opening the door to new possibilities in medical technology with each advancement.
Designing with Nitinol
At Resolution Medical we know how to harness Nitinol’s unique properties to meet your clinical needs, with thoughtful integration into any catheter-based system you can imagine. As a full-service contract developer and manufacturer, we approach Nitinol not merely as a component but as a pivotal part of a medical device system.
Our Nitinol experts are well versed in this unique material and have developed a wide breadth in the medical device industry which allows them to better design for system integration, anticipate clinical implications and plan for today’s complicated regulatory currents. This depth of knowledge has been cultivated through years of collaboration with innovative startups and we’re honored to bring this experience to your project.
At Resolution our team becomes your team, proactively guiding you through each step and anticipating challenges to manage a smooth path from concept to clinical studies.
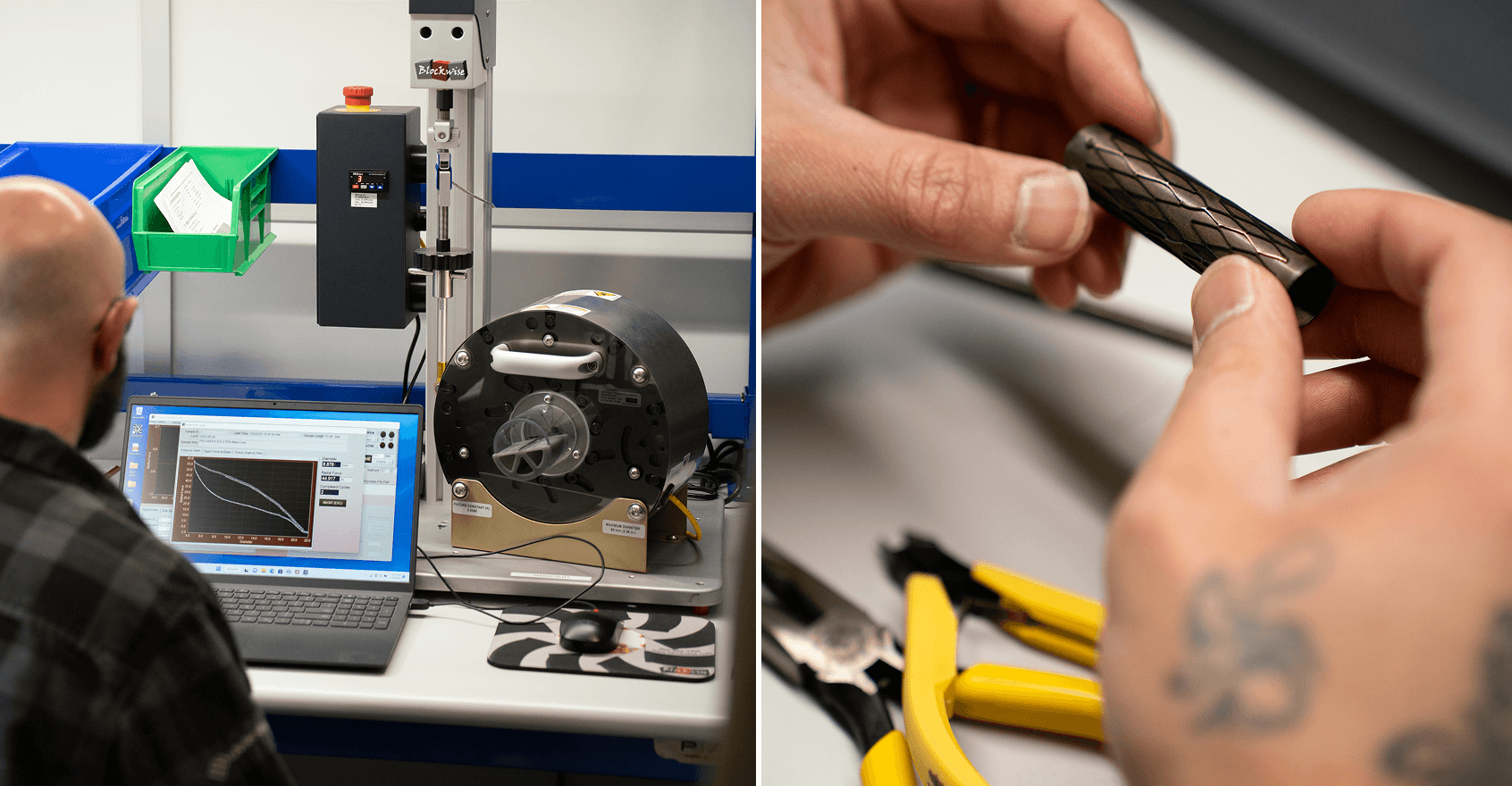
Processing Nitinol
Nitinol components have a lot of requirements placed on them to achieve a successful clinical product, all of which are sensitive to the design and control of the unique processes used to fabricate these intricate structures. These processes need to be adapted to each frame and their specificity needs to grow with the project to ensure flexibility in early stages when you need to be nimble and controlled in late stages when you need consistency.
Our engineers take processing into consideration from the start of your project, anticipating controls needed for each stage of development and laying an efficient path to a robust component.
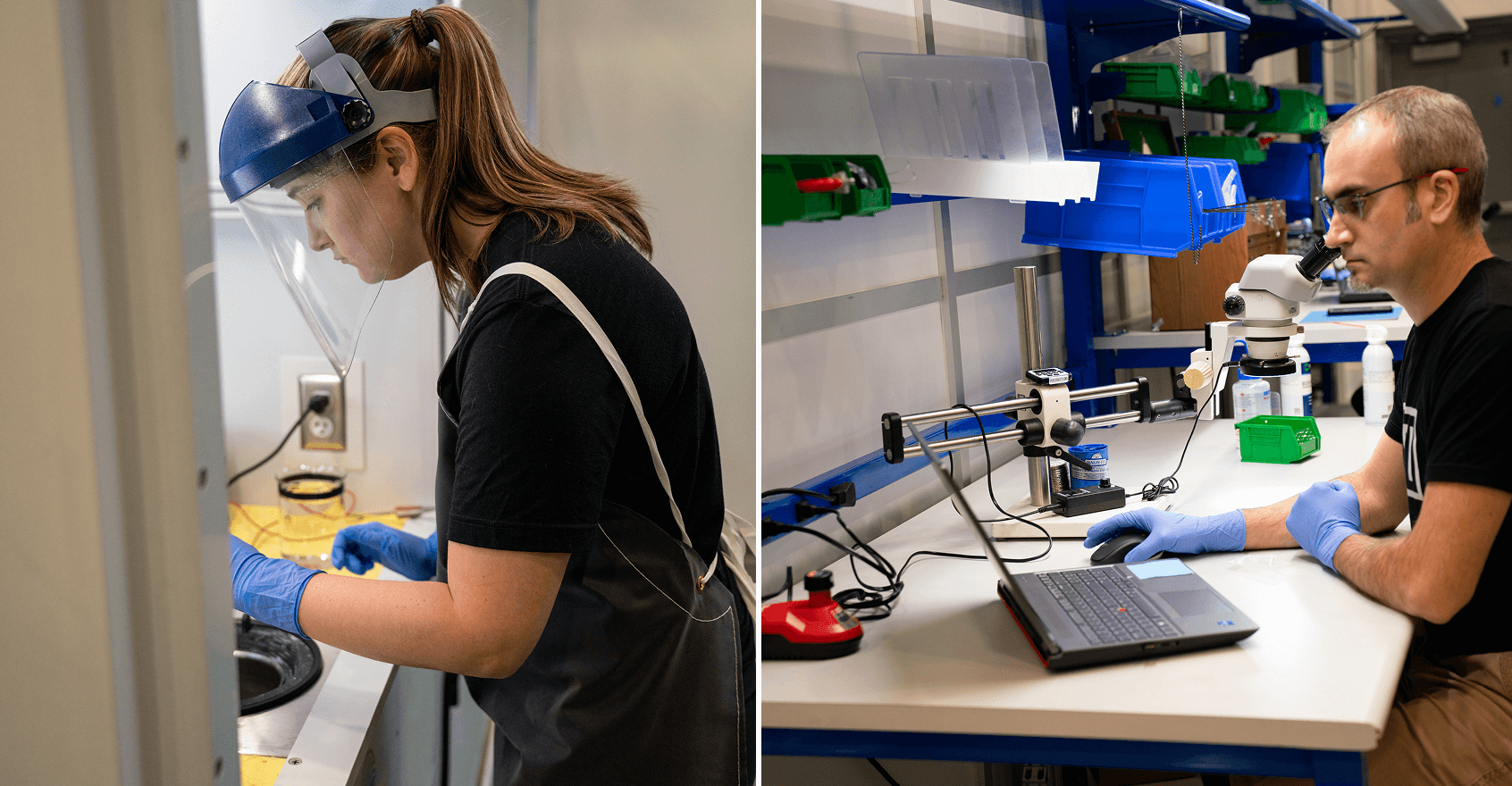
Comprehensive In-house Capabilities for Nitinol
Design: Application & design expertise specific to Nitinol, including design, engineering, manufacturing, and end use functionality.
Laser Cutting: In-house femto and fiber laser cutting for tube and flat sheet materials.
Shape Setting: Constraining the Nitinol components to the fixture and heat treat to permanently set to the desired shapes. Our NiTi team specializes in fixture design to accurately and efficiently shape set Nitinol components.
Electropolishing: Our electropolishing process smooths Nitinol surfaces, enhancing corrosion resistance, fatigue resilience, and biocompatibility for medical applications; this makes the components more durable and safer for use.
Passivation: We offer passivation to Nitinol components to form a passive and biocompatible Titanium oxide layer.
Testing Capabilities: Our in-house testing capabilities enable us to respond swiftly to the results by refining designs and processes, at every stage.
- Contact Af Test
- Non-contact Af Test
- Coupon Tensile Test
- Radial Force Test
- Bench Testing of the whole device
- BioSim Test
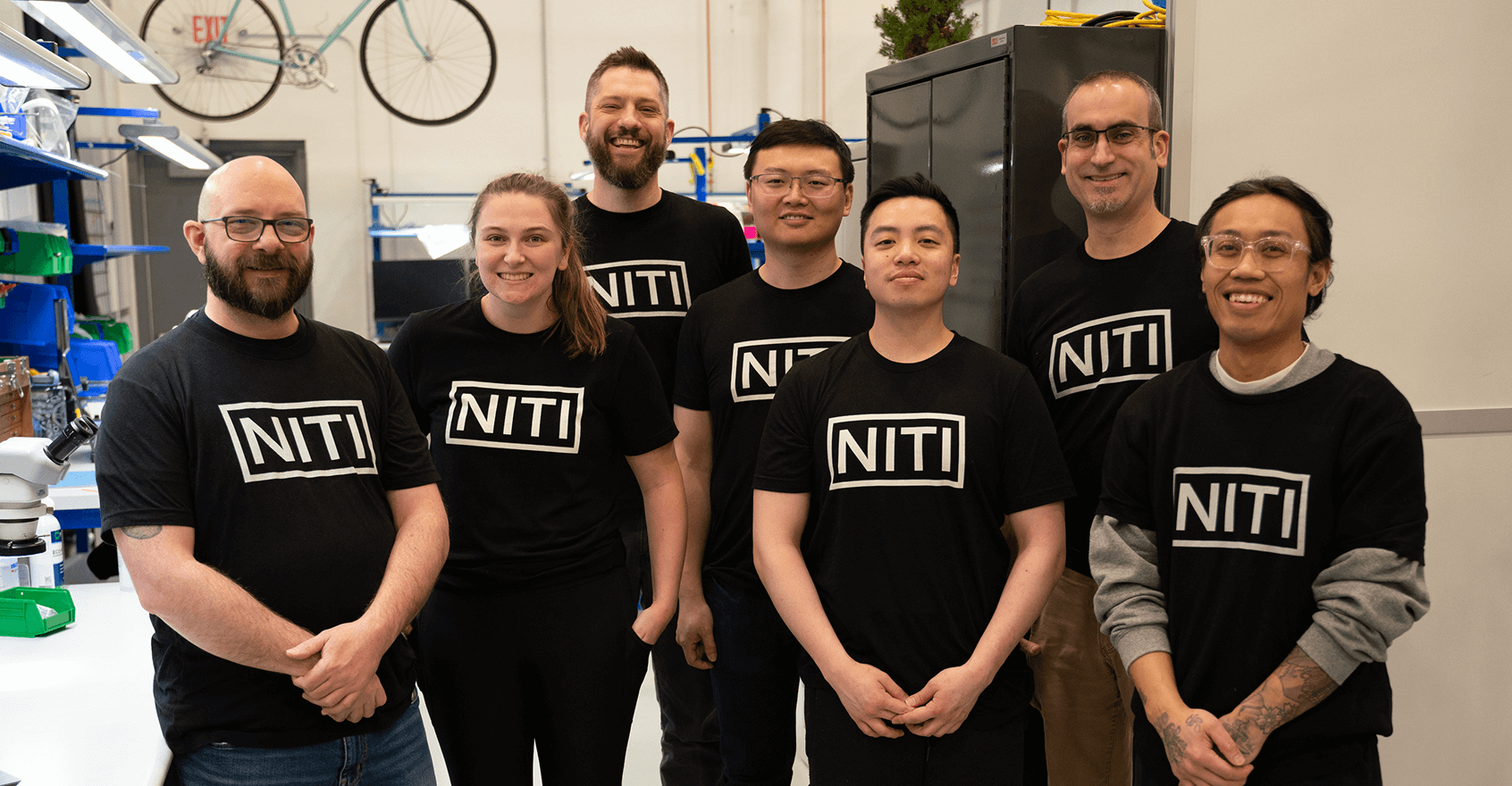
Your Comprehensive Partner
Our Nitinol team has a genuine passion for working with this material that has transformed how we see metals in medical devices. At Resolution Medical, we are able to apply our passion to co-create innovative solutions with you and your team. Collaboration is the secret to our success. Nitinol represents the future of medical materials and we’re here to help you harness its full potential.